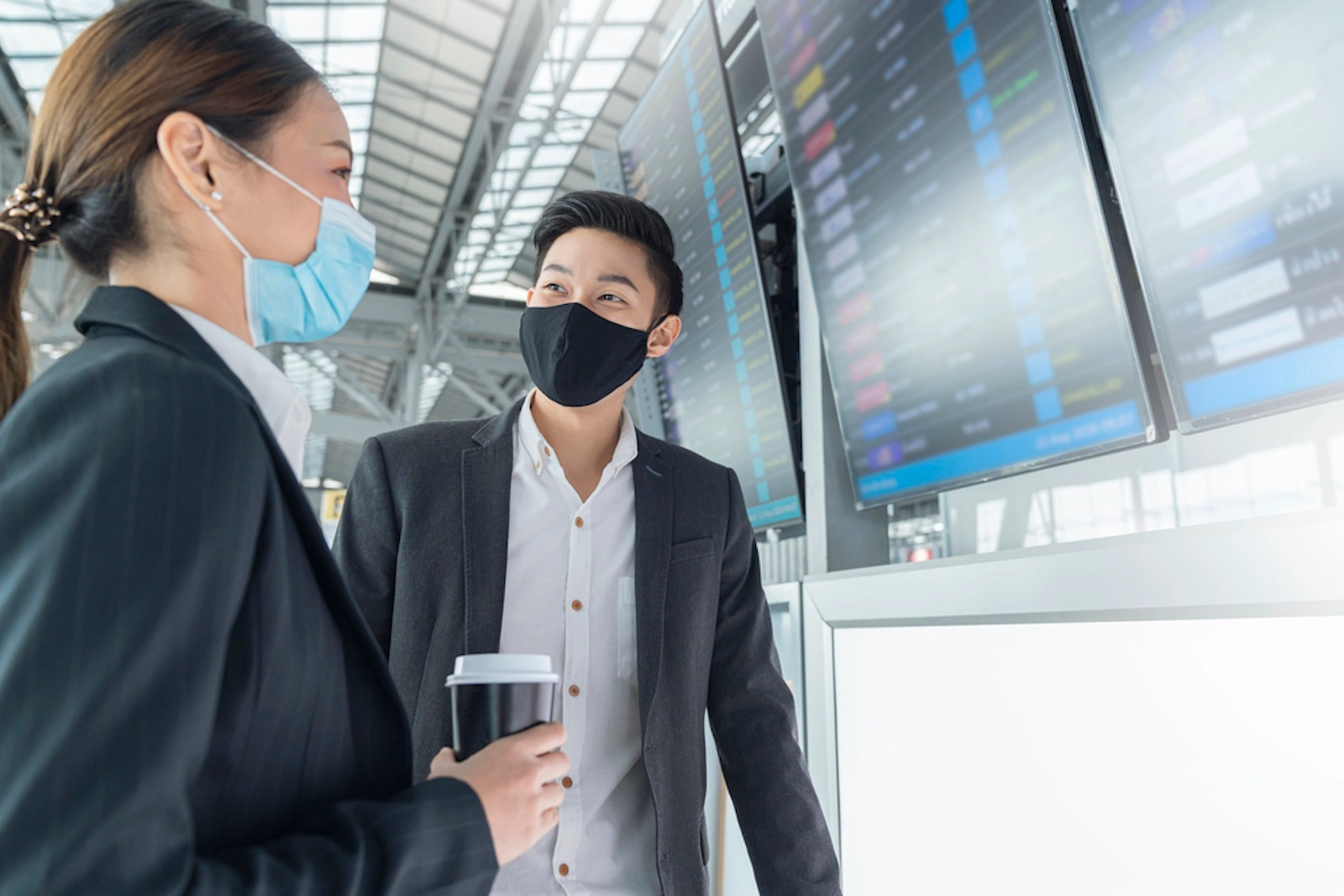
How Digital Signage Manufacturers Ensure Product Reliability
May 22, 2024
In today's tech-driven world, digital signage has become an integral part of many industries, from retail to transportation. One sector where digital signage plays a critical role is manufacturing.
Ensuring the reliability of these digital signs is paramount, and this responsibility falls on digital signage manufacturers. This article explores how digital signage manufacturers guarantee product reliability, focusing on digital signage for manufacturing and its specific quality control processes.
The Importance of Quality Control in Digital Signage Manufacturing
Quality control is essential in the production of digital signage. It ensures that the products meet industry standards, perform reliably, and provide a positive user experience. For digital signage in manufacturing environments, reliability is particularly important due to the demanding conditions and continuous operation requirements.
Rigorous Testing Procedures
Digital signage manufacturers implement rigorous testing procedures to ensure product reliability. These tests cover various aspects of the signage, including hardware durability, software performance, and overall functionality.
Environmental Testing
Environmental testing is crucial for digital signage used in manufacturing settings. These signs must withstand extreme temperatures, humidity, dust, and vibrations. Manufacturers conduct tests in controlled environments to simulate these conditions and ensure the signs can operate effectively under such stresses.
For instance, they might expose the digital signs to prolonged periods of high heat or cold to see if the components continue to function correctly. Vibration tests mimic the constant movement found in many manufacturing plants, ensuring that the signs remain stable and operational.
- Temperature Testing: Signs are exposed to high and low temperatures to ensure they operate in various climates without malfunctioning.
- Humidity Testing: High humidity levels can cause condensation inside the signage. Testing ensures the signs are sealed properly to prevent moisture damage.
- Dust Resistance: In dusty environments, digital signs must be sealed to prevent dust from infiltrating and damaging internal components. Dust resistance testing ensures the longevity of the signage.
- Vibration Testing: Manufacturing environments can be subject to significant vibrations. Signs are tested to withstand these vibrations without degradation in performance.
Performance Testing
Performance testing involves evaluating the software and hardware components to ensure they function correctly. This includes checking the display quality, response times, and system stability. By thoroughly testing these elements, manufacturers can identify and address any potential issues before the products reach the market.
- Display Quality: The clarity, brightness, and color accuracy of the display are tested to ensure high-quality visual output. Any anomalies, such as pixel failures or color distortions, are addressed.
- Response Times: This involves testing how quickly the signage responds to input commands. Rapid response times are crucial for interactive displays and ensuring a smooth user experience.
- System Stability: The overall stability of the system is tested by running the signage for extended periods. This helps to identify any potential issues that could cause the system to crash or malfunction over time.
- Software Functionality: The software running the signage is tested for bugs, compatibility issues, and overall performance. This ensures that the software integrates seamlessly with other systems and provides a user-friendly interface.
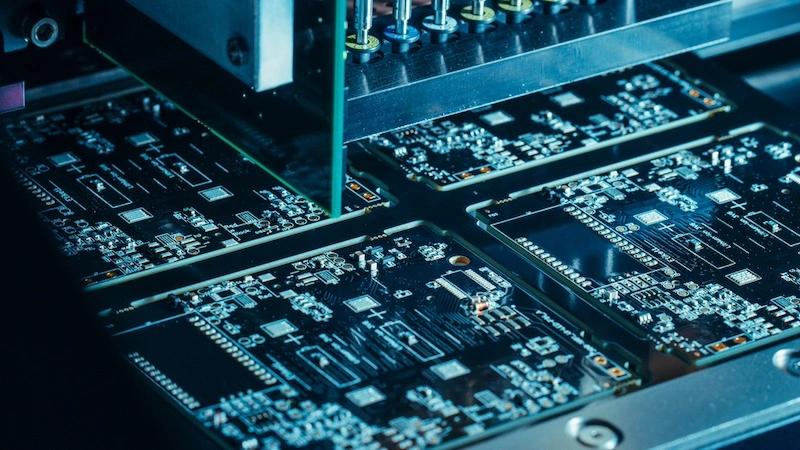
Quality Control Processes for Digital Signage Manufacturers
Digital signage manufacturers follow a series of quality control processes to maintain high standards. These processes include design validation, production monitoring, and post-production testing.
Design Validation
The first step in ensuring the reliability of digital signage for manufacturing is design validation. This involves verifying that the product design meets all required specifications and standards.
- Prototyping - During the prototyping phase, manufacturers create a working model of the digital sign. This prototype is tested extensively to identify any design flaws or areas for improvement. Feedback from these tests is used to refine the design before full-scale production begins.
- Compliance Checks - Manufacturers also conduct compliance checks to ensure that the digital signage meets industry standards and regulations. This includes checking for electrical safety, electromagnetic compatibility, and environmental impact. Compliance with these standards is critical for ensuring the reliability and safety of the final product.
Production Monitoring
Once the design is validated, the focus shifts to monitoring the production process. Consistent quality control during production helps prevent defects and ensures that each unit meets the required standards.
- Automated Inspection Systems - Many digital signage manufacturers use automated inspection systems to monitor the production process. These systems use advanced imaging and sensor technologies to detect defects in real time. By identifying issues early, manufacturers can address them before they affect the final product quality.
- Quality Audits - Regular quality audits are conducted throughout the production process. These audits involve inspecting random samples of the digital signs to ensure they meet the specified criteria. Any deviations are recorded and corrected to maintain consistent product quality.
Post-Production Testing
After the digital signage units are produced, they undergo post-production testing to verify their reliability before shipment.
- Burn-In Testing - Burn-in testing is a crucial part of the post-production process. It involves operating the digital signage units continuously for an extended period to identify any potential failures. This test helps ensure that the signs can handle the demands of a manufacturing environment without issues.
- Final Inspections - Before the digital signage units are shipped, they undergo final inspections. These inspections include checking the physical appearance, verifying the functionality, and ensuring that all components are correctly assembled. This final step helps guarantee that the products delivered to customers are of the highest quality.
The Role of Digital Signage in Manufacturing
Digital signage plays a significant role in manufacturing environments. It helps improve communication, increase efficiency, and enhance safety. Reliable digital signage is essential for these benefits to be realized.
Enhancing Communication
Digital signage in manufacturing displays important information such as production schedules, safety instructions, and real-time performance data. Clear communication impacts productivity and safety.
Up-to-date schedules ensure that all employees are aware of their tasks, reducing confusion. Safety reminders help ensure compliance with regulations. Real-time performance data keeps workers informed, driving motivation and accountability.
Increasing Efficiency
Real-time updates and alerts from digital signage streamline operations. Digital signs can display machine status, production targets, and maintenance schedules, allowing workers to respond quickly to changes or issues.
Knowing the operational status of machinery is crucial. Digital signs indicate whether a machine is running, idle, or needs maintenance, minimizing downtime. Displaying production targets keeps workers focused. Maintenance notifications ensure timely servicing of machinery, reducing the risk of breakdowns.
Improving Safety
Safety is a top priority in manufacturing. Digital signage displays critical safety messages, emergency instructions, and hazard warnings. Reliable digital signs ensure effective communication of important messages, maintaining a safe working environment. Continuous reminders about personal protective equipment (PPE) and safety protocols help prevent accidents.
In emergencies, digital signs provide clear instructions on evacuation routes and procedures, ensuring a swift response. Digital signage can also alert workers to temporary hazards, reducing the risk of accidents.
Additional Benefits
Digital signage is useful for training and onboarding new employees. Interactive displays guide new hires through safety procedures, operational protocols, and company policies, ensuring they are well-prepared.
Recognizing employee achievements through digital signage boosts morale. For facilities that host visitors, digital signage provides important information such as maps, schedules, and guidelines, enhancing the overall experience.
Conclusion
Digital signage manufacturers play a critical role in ensuring the reliability of their products, particularly for use in manufacturing environments. Through rigorous testing, design validation, production monitoring, and post-production testing, these manufacturers ensure that their digital signs meet the high standards required for reliability and performance.
As technology continues to advance, digital signage for manufacturing will become even more integral to improving communication, efficiency, and safety in the industry.
Get Started
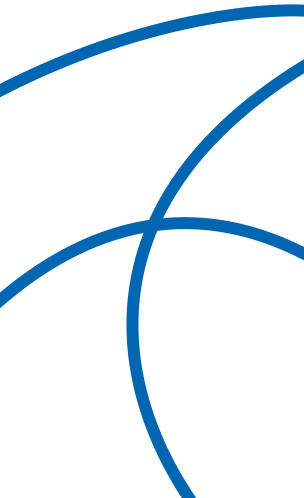